A307 headed bolts are most commonly manufactured in one of two ways: cold forging or hot forging. Both of these processes create similar end products but how they are manufactured is completely different.
Cold Forging / Mass Production
- Cutting
When cold forging, the raw material starts as a long coil of wire which is then fed through a machine to be straightened before the parts are cut to length. The straightening process prevents the parts from having any deformations or slight bends in the steel which can cause weaknesses in the final product. Once the material has been straightened, the wire is sheared into sections slightly longer than the required bolt length in order to forge the bolt head with the excess. - Heading
Once the material has been straightened and cut to length, the parts are fed into a series of dies which form the head of the bolt. Because the material is formed without heating the steel it is referred to as “cold forging.” The head of the bolt is shaped through multiple die hits at room temperature which ultimately creates the head shape. This process is so efficient that tens of thousands of bolts can be manufactured in a single day. - Threading
When the heading process is complete, the opposite end of the bolt is threaded. Cold-headed bolts are threaded through a roll-threading process where two flat threading dies roll or form the threads of the bolt. The shank of the bolt is extruded down to a pitch diameter and then fed through the dies where the threads are formed.
Hot Forging / Custom Manufacturing
- Cutting
When a headed bolt is hot-forged, the cutting process begins by cutting the raw steel to the appropriate length. Typically, the steel round bar is hot rolled in lengths of 20 feet or longer which is then cut down to size. Similar to the cold-forged fasteners, the cut pieces are longer to accommodate the extra material needed to forge the bolt head. - Heading
After the steel has been cut to length, one end of the rod is heated up through an induction process and then forged in a National Upsetter. The upsetter has a plunger that compressed the heated steel to form the bolt head along with the required grade stamp and manufacturer’s logo displayed on the surface of the bolt head. Presses can also be used to hot-forge bolt heads. - Threading
Once the fasteners have been headed, the opposite end of the bolt is threaded. Hot-forged fasteners can be roll threaded just like cold-forged bolts, however, they can also be cut thread. Cut threading is a process where steel is physically cut away from the body of the bolt to form the threads.
Bent Bolts
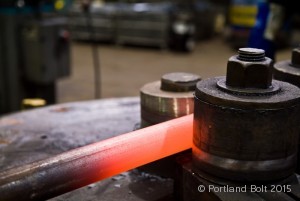
The A307 specification allows for many different styles of bent fasteners. The fasteners include round and square U-bolts, eye bolts, and round and square hook bolts. When these parts are bent, the round bar can be heated up to create tighter bends or bent at room temperature.
Threaded Rods
Another common type of A307 fastener is threaded rods. Threaded rods can be made in several ways: fully threaded, threaded on each end, and threaded on one end. There are multiple uses for different types of threaded rods across every industry. A307 is one of the most common grades used for threaded rods in the marketplace.